Gas pressure regulators, are used to ensure that the amount of gas leaving a high-pressure cylinder is at a safe and workable level for operating equipment and instruments. While they are commonly used for industrial applications such as welding, gas regulators are found on everything from gas grills to engines and dental equipment.
There are a few main types of regulators like Single stage and Multi stage, and our guide is here to break them all down.
Single stage
As the name suggests, Single stage gas pressure regulators work in one stage to reduce the pressure leaving the cylinder through an outlet. When noting the differences between Single stage and Multi stage, it is also important to know about droop and supply pressure effect. Droop is used to describe the difference between zero pressure and the maximum amount of flow capacity in the gas regulator. Supply pressure effect, or dependency, is the variation in outlet pressure and the inlet pressure changes, or in simpler terms, occurs when the pressure changes as the cylinder empties.
Single stage regulators are recommended for uses where there will be less fluctuation in pressure or where readjustments of pressure are not an issue.
Multi Stage
Unlike Single Stage regulators which have less droop but a greater pressure effect, Multi Stage regulators show more droop but a smaller pressure effect. Multi stage regulators are also recommended for uses where pressure needs to be constantly delivered and not be adjusted.
A supply of constant pressure is one of the main advantages of using a Multi stage regulator as when gas leaves a gas cylinder, the pressure in the cylinder drops. As this happens, Single stage regulators show a ‘decaying inlet characteristic’ where the pressure increases as the inlet pressure decreases. Multi stage regulators compensate for this by providing a constant delivery of pressure regardless of the inlet pressure.
High Pressure
Simply put, high pressure gas regulators are designed to deliver high gas delivery rates. High pressure regulators can be either Single stage or Multi stage and are used with equipment where a high heat output is required.
Nevoc
Nevoc, which stands for New European Valve Outlet Connections, refers to a type of valve fitting that is designed to safely reduce the pressure from 300bar to lower levels for more efficient industrial operations. Nevoc gas pressure regulators like the Nevoc Ga600 2 Stage High Pressure Regulator are used in instances where stable outlet pressure is required and is ideal for a variety of cutting applications like heavy machine cutting and precision cutting.
ESAB EDGE Regulators
ESAB EDGE regulators come in both single and multi-stage versions for a variety of applications. They feature unique ESAB Slam technology which protects critical regulator components and the cylinder in the event of a fall, absorbing up to 5000lb of impact energy which could otherwise cause damage and potential risks with other regulators on a full gas cylinder.
ESAB EDGE regulators also deliver better flow control and a more consistent supply of gas across a range of pressures, even when cylinder pressure decay occurs.
When choosing a gas regulator, it is important to note that they have a use by date, as do other pieces of equipment like gas hoses, so you should always check your equipment to ensure safe usage. Something else to consider is where the entry point is for the regulators as different gas bottles can have either side or bottom entry where the valve is located.
Which regulators are used for which types of welding?
Whichever type of welding you are carrying out, it is essential that you get the right regulator for the job. Not only is it important because different regulators have different screw threads, such as regulators for combustible gases like Acetylene and Propane usually having Left Hand Threads, but using the wrong regulator can also be dangerous.
- For MIG & TIG welding, the type of regulator you use depends on the mix of gas you’re using, with the most commonly used regulators being Argon & Inert gas regulators. When TIG welding, we also recommend using a flow meter which is designed for use with shielding gases used in TIG welding applications. Flow meters not only greatly increase the accuracy of the gas flow control when fitted to an argon regulator, but have the added benefit of giving a visual indication of when gas is actually flowing.
- For Oxy or Acetylene welding you will also need an oxygen regulator and an acetylene regulator for each gas cylinder.
What are flashbacks and why are they a risk?
A flashback is a rapid, high-pressure flame which travels back up the gas hose. These are caused by a number of factors such as welding or cutting at incorrect pressure settings, from a blockage or overheating of the nozzle, for example by operating with the nozzle too close to the material.
Flashbacks can result in extremely dangerous cylinder ignition and must be prevented by proper use of working Flashback Arrestors.
Related Categories:
- Single Stage Gas Regulators
- Multi Stage Gas Regulators
- Nevoc Gas Regulators
- High Pressure Gas Regulators
- Butane / Propane Gas Regulators
We can even supply the welding gas you need through Energas, just get in touch to find out more.
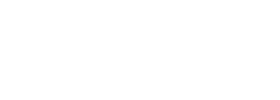