It has been 12 months since updated health and safety regulations were released by HSE following the reclassification of mild steel welding fumes as a human carcinogen. HSE have recently released another updated best practices guide on welding fume extraction. Engweld, the suppliers of premium engineering and welding products, have summarised the update to highlight the key changes to customers.
New enforcement expectations require all businesses undertaking welding activities to ensure that effective engineering controls are provided and used correctly to control fumes arising from welding activities. It is now advised that larger fume producing welding types such as MIG & MMA require a double pronged defence of respiratory protective equipment (RPE) and local exhaust ventilation (LEV).
Lower fume producing welding, such as TIG usually only requires LEV protection, however it is advised that in applications where it is not clear whether LEV is providing sufficient fume control, that LEV and RPE are used conjunctively for maximum protection.
There is not a “one size fits all” solution for every welding type and application, and so it is advised that an occupational hygiene air monitoring survey may be required to confirm the effectiveness of fume controls.
While on-torch extraction solutions can provide effective fume control, workers should be aware of the limitations of this method, as with all fume extraction methods.
It is also reccommended that welders use a PAPR (Powered Air Purifying Respirator) Unit if they’re welding for over one hour per day.
LEV supervision and training is highly recommended by the HSE to ensure that workers know how to effectively use LEV, how to check it is working efficiently, and to ensure they are following safe working procedures.
Finally, all fume extraction equipment should be routinely serviced and maintained to be in good working order. Filters should be regularly changed on PAPR units and on-torch units, and a ventilation engineer should carry out LEV testing every fourteen months. All checks and maintenance should be routinely recorded in a log book.
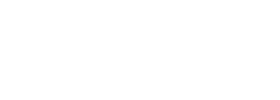